Introduction
Metis Energy LLC is a dynamic Texas Exploration & Production company with multiple, remote well sites along the southern Texas border. Currently, their wells require daily Pumper inspections. It takes Pumpers 46 miles and two hours per day of roundtrip travel, costing $1,300 per month to conduct manual gauging and equipment review. With the Metis Operations manager located over 300 miles from their wells, Metis was faced with the challenge of how they could lower costs and gain more real-time insights using technology to monitor well production, tank volumes, and daily operations.
Metis Energy trialed Machfu’s well site monitoring system in conjunction with Machfu’s services partner, Team International to remotely monitor the Carrizo Spring site. The no-cost trial included:
- Business and site assessment – What data is critical for operations management? What sensors should be deployed at the site to realize maximum efficiency gains and cost savings?
- Web-based Dashboard review – What type of data, the frequency at which the data is needed, and how to present it in the best way to be immediately useful for operations? For example, tubing and casing pressure and tank levels was determined to be critical information.
- Field Installation of sensors and communication devices, and provisioning devices for reporting to the cloud and dashboard
- Data collection, storage and dashboard user acceptance testing
- Start of trial and continual sensor, data and user support services
- Post trial assessment and development of an approach for full rollout.
Metis Energy projects that the benefits of Machfu remote monitoring will reduce direct costs by $8,400 per year at each wellsite and lead to operational efficiencies that result in revenue gain of $11,000 annually. The automation cost to Metis is less than $200 per month or a mere 15% of Metis Energy’s net profit gain.
1. Situation
Like thousands of other small and mid-sized E&P Operators, how could Metis energy scale, sustain and optimize its remote operations across the South Texas expanse? The manual process posed cost as well as safety and accuracy risks, and a typical response time to HSSE or Operational events at the well sites was 24-30 hours. Traditional SCADA systems were too costly and outdated to adopt into this agile, growing company. In June 2021, Machfu approached Metis Energy for a trial, a consideration and priority that had not been part of Metis’ 2021 operations and technology plan for its current and new acquisitions of well sites.
Metis signed up for a 60-day Machfu trial with these objectives:
- Gain insight into breadth and detail of data via remote technology
- Measure the tangible benefits of remote monitoring
- Gauge the accuracy and timeliness of well equipment data
- Determine how the data could be used to reduce site inspection and logistical costs and risks and improve production uptime
- Assess if the technology was scalable and a value add to Metis and working interest partnerships
- Determine if Machfu provided a competitive advantage vs. other small E&P Operators
2. Trialdesign
Metis Energy worked alongside Machfu and Team International to determine the critical operational data, and the type and placement of sensors and measurement units. The team agreed to install nine sensors:
- 1. Two tubing and two casing sensors on each of the Palosa 3H and 5H wells
- 2. Two sensors on each of the 3H and 5H Pump Jacks
- 3. One sensor on the single stream Heater Separation Unit
- 4. Two sensors on each of the Water and Oil Frac tanks
Sensor data was captured by the MachIO and Machfu IoT gateway. These data points were then displayed on the Metis Energy LLC Dashboard to provide a complete operational picture of the site. Water and Oil Frac tank levels were of special focus to detect tank overspill and to optimize timing for water and oil loading and transportation.
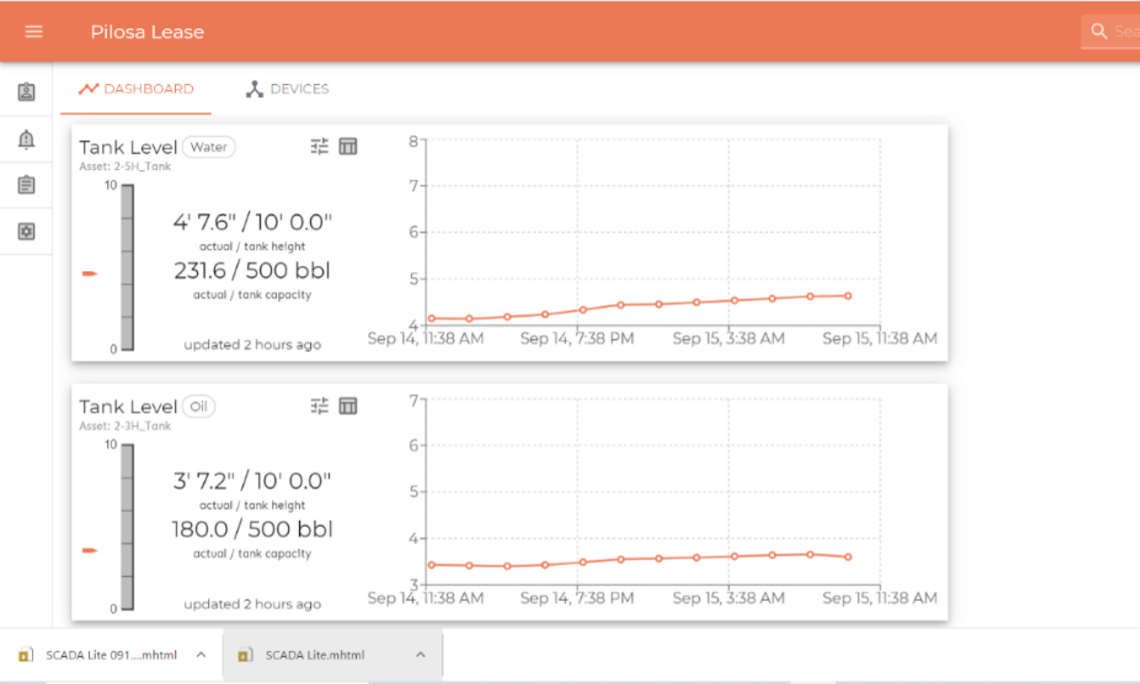
3. Trial Results
The ease of installation is one of the most attractive features of the Machfu automation system. An installation at a typical well site which consists of a tubing and casing pressure, tank level sensor and a heater sensor can all be completed in under 2 hours. This time includes commissioning the system and verifying that data is being reported to the dashboard for viewing. After the physical installation of devices, a Smartphone APP is used to provision all the devices and connectivity to the cloud. The App is a powerful tool that significantly speeds installation and provides on site diagnostics needed for rapid completion. The phone will show the installer all the MachIO and sensors installed along with diagnostic and system information.
The Metis dashboard extrapolates tank readings from the tank volume levels and specific gravity of the liquids. Oil shipments can be planned once oil volume reaches over 200 barrels and water volume at 300 barrels or greater. Data is captured every two hours – appropriate for low volume daily production. Data from seven other outputs were captured as part of the Metis Energy LLC location wellsite and made available in the main menu dropdown.
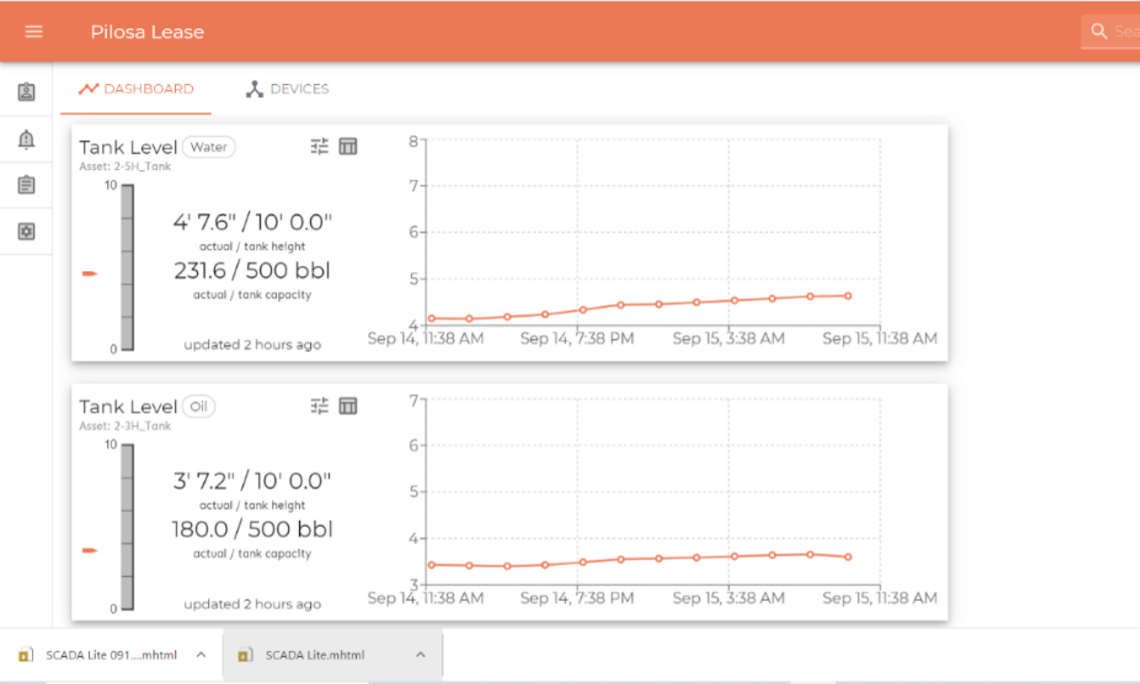
Below is the actual readout of Tubing and Casing pressures from September 16, 2021. This data captures downhole tubing pressure and casing flow pressure, evidence of continual operations. Metis has set thresholds on its dashboards to trigger alarms when pressures indicate exception readings. The local site inspector gets notified of these exception events on their cell phone prompting an immediate corrective response which is an improvement to the previous 24-hour lead time for a scheduled inspection. The specific benefits achieved in this pilot are:
- Lower hours of production downtime: Maximum response time of 2-3 hours to alarms
- Reduction of pumper site inspection from 7 to 3 times per week: 30% lower pumper cost, drive miles expense, and safety risks
- More frequent adjustments to heater separation: greater oil/water separation
- Lower risks of tank environmental incidents (overflows): tank capacity alarms
- More timely oil shipments sales: scheduled when full T/T volume and highest PBP
- Reduced water loading and disposal rates: scheduled at low peak times
- Potential reduction in oil theft: oil tank volume monitoring and site surveillance
Future functionality will also enable remote equipment shutdown, and is currently in development.
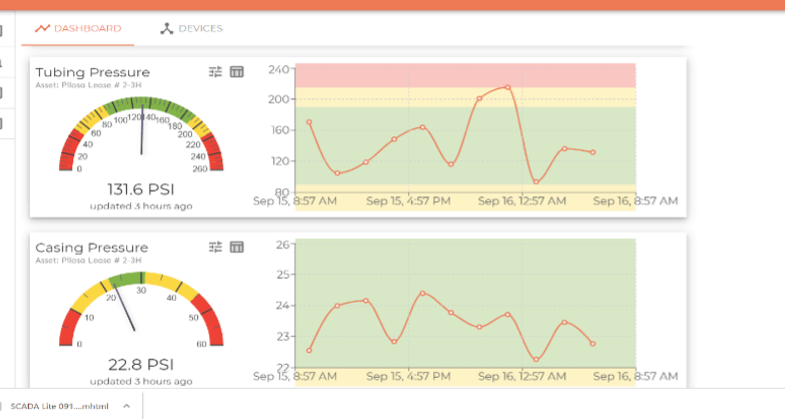
4. Network Health Monitoring
While the customer has views of well site operation through the Web-based Dashboards, the service package also includes continuous performance monitoring of the automation system including alerts for failed communications, continuous checks on sensor health, battery capacity monitoring to predict in advance for change outs and maintenance etc. for a full view of system and network performance. The Machfu device management dashboard is shown below.
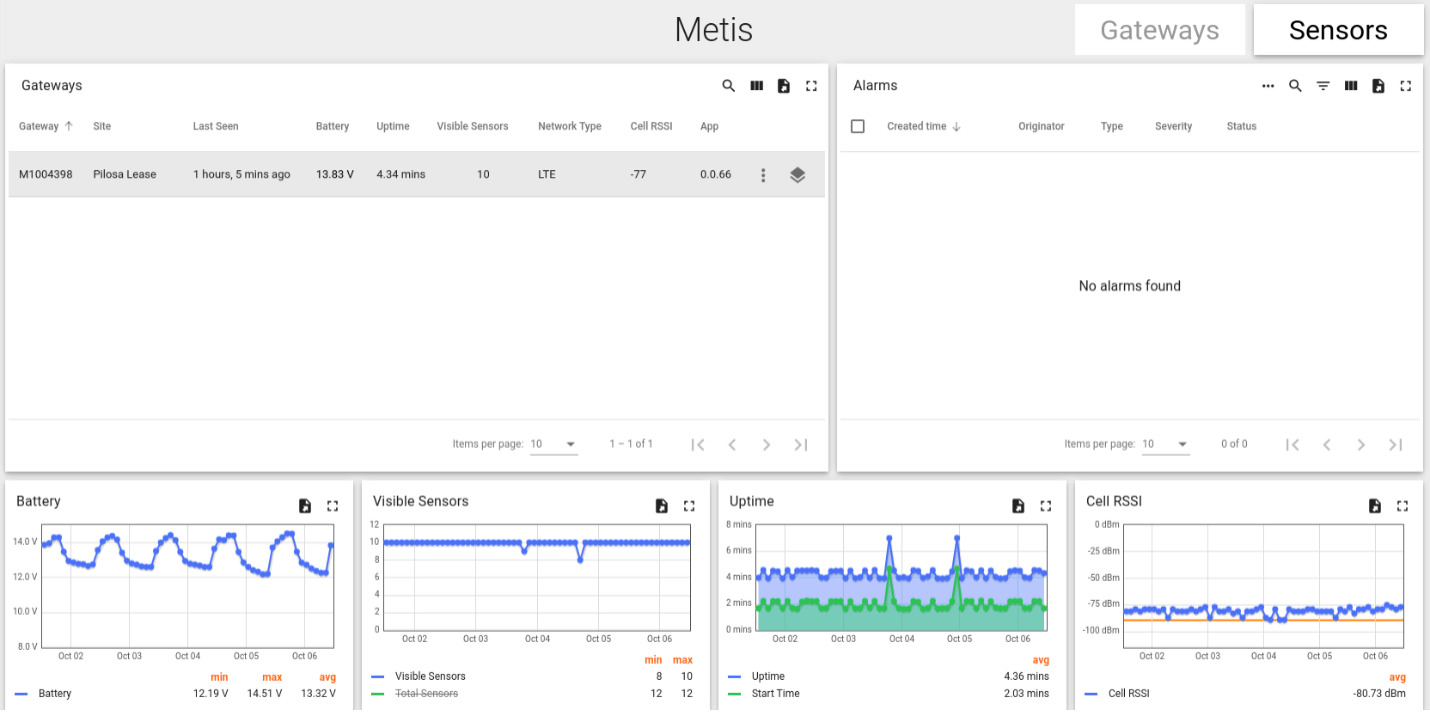
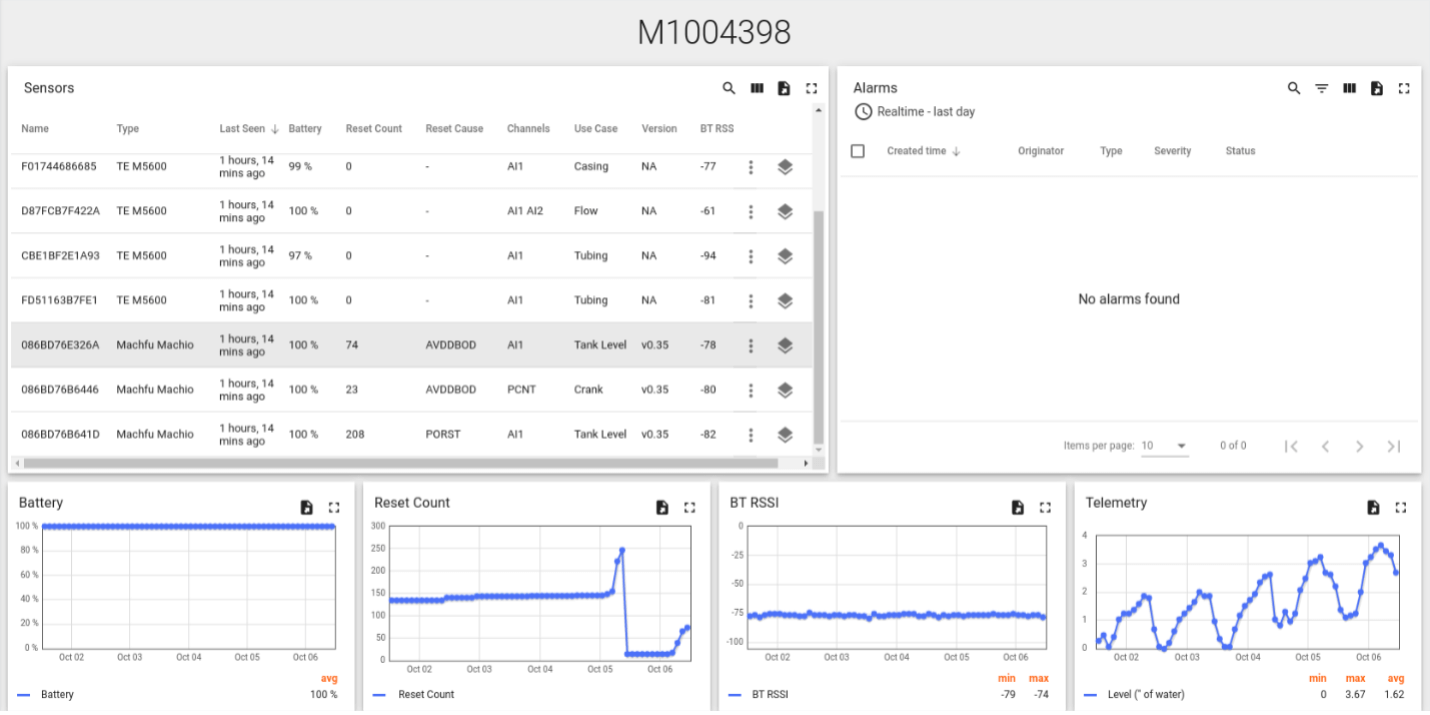
As part of the service offering, Machfu provides a cloud based chatbot application that is used for quickly retrieving key pieces of information about the deployed system using popular messaging and social media smartphone apps.
Such information includes (but is not limited to) the following:
- The overall health of the system (i.e., list of all sensors, gateways and sites that are currently experiencing communication or battery issues)
- The count and identifiers of all deployed gateways and sensors for a customer
- Parameters such as battery levels, cell signal strength etc. of the gateways and sensors
- The list of sensors that are currently in the communication range of a particular gateway
- More timely oil shipments sales: scheduled when full T/T volume and highest PBP
- Reduced water loading and disposal rates: scheduled at low peak times
- Potential reduction in oil theft: oil tank volume monitoring and site surveillance
The chatbot functionality is available to the field installation personnel using the popular Slack messaging app, available on all Android and iPhone devices. This is extremely useful in situations where time is of the essence and navigating the Network Health Monitoring portal to retrieve the desired information may be cumbersome. Such situations routinely arise during field installations where information such as "the number of sensors currently in the range of the gateway" needs to be retrieved after each sensor/gateway is deployed. The field environment is often hot, humid and with bees and other insects flying and rapid time to completion is vital.
5. Results
Metis Energy has integrated Machfu’s remote technology into its operations management already. Metis Energy anticipates meeting its projections of reducing direct costs by $8,400 per annum and increased revenue gain of $11,000 per annum. The automation cost to Metis is less than $200 per month or 15% of Metis Energy’s net profit gain.
It will be expanding to the Eagle Pass well site and adding video cameras to both sites. Metis Energy is adding contractual terms for remote well monitoring to three Working Interest Partner agreements as of September and October 2021. Simply stated, Metis Energy will fully adopt Machfu technology into their strategic plans. The expected immediate results will be:
- 1. Reduced operational costs
- 2. Improved uptime and operational planning efficiencies
- 3. Lowered HSE risks and improved security over oil theft and or site intrusion
- 4. Improved partner management and data control
- 5. Visibility to current Metis Energy Investors
Metis Energy will deploy Machfu remote monitoring spanning West Texas to North Texas to the Texas Panhandle. There will be a single Metis Energy dashboard with each well site listed, and under each site, the various sensor data displays. This data will be accessible to Metis Energy staff, working interest partners project staff, and select investors.